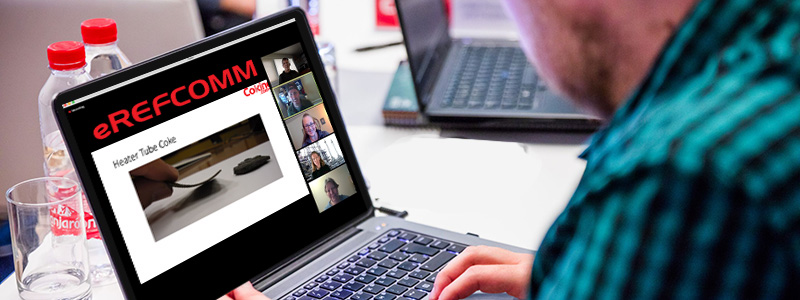
What do you want to talk about? Bring your process and troubleshooting issues to this session. Discuss and collaborate with your DCU colleagues from around the globe. What do you want to talk about? Bring your process and troubleshooting issues to this session. Discuss and collaborate with your DCU colleagues from around the globe. Actuation and controls on critical service FCC valves have evolved over decades becoming more and more complex. Process licensors have continued to modify their specifications based upon industry feedback and their own research. What do you want to talk about? Bring your process and troubleshooting issues to this session. Discuss and collaborate with your DCU colleagues from around the globe. Some refiners operating an (R)FCC sell their residue from the Fluid Catalytic Cracking Unit as bunker fuel blended into a fuel pool. This is especially attractive when used for blending down Sulphur content of bunker fuels. Refiners are facing significant challenges including a historic reduction in fuels demand and the early impact of IMO 2020 regulations. However, long-term forecasts show… Testing of FCCU main Blower and Wet Gas compressor Control System is always a challenge as all tests and verifications at vendor premises are performed on Simulation mode, without actual compressor or Blower. Essential to re-using metal filters is understanding cleaning methods for removing asphaltenes, organics, and inorganic catalysts fines/sulfur from metal filters, along with, testing methods that quantify the media cleanliness. Bringing the filter media matrix back to a ‘like new’ condition will minimize or eliminate the typical issues related to inadequate cleaning. FCC units process heavy gas oil or vacuum gas oil (HVGO) and convert them into much more valuable gasoline. Pressures are moderate, not exceeding 30-40 psig. Temperatures are very high, and in certain parts of the process can approach 1450 deg F. The “magic” of the FCCU is mostly contained with the catalyst that is utilized. Delayed Coking Ancillary Equipment (Blowdown System, Coke Cutting, Coke Handling, and Water Handling) Facilitator: Sim Romero, Becht Engineering Overview How long do you steam out to the fractionator and with… speaker: Vahe Avetisyan, VVInEx GmbH Discussion Topics: Different Approaches to Project QA/QC affecting final results DCU Major equipment and specifics in regards to QA/QC activities QA / QC Matters and… Collaborate with plant personnel to achieve sustainable, pacesetting operational excellence by guiding and coaching them consistently applying their unique strengths to implement leading edge reliability best practices. Voovio Technologies and customers will discuss the challenges of executing SOPs in the field, unplanned events, on-boarding new hires, refresher training, and job re-qualification, which have been exacerbated by the pandemic. Delayed coker units (DCU) are more sensitive to insulation performance than any other process unit in a refinery. In this webinar, we’ll discuss how the choice of thermal insulation in a DCU can make an impact. TUBACOAT (or advanced ceramic coated tubes) is a disruptive innovation technology from TUBACEX Group. This new technology of silica ceramic coating has an excellent resistance to coking, erosion and corrosion at extreme conditions and high temperature up to 800oC(1472oF). In this webinar, Refined Technologies will discuss proven methods for improving the operability of coker ball valves and other dynamic equipment. This will allow longer operation by using chemistry alone. One of the things that I’ve been seeing a lot in the past five years is what I like to refer to as “The Farmer Fix.” The Farmer Fix is when hydraulics are leaky and somebody puts a five-gallon bucket underneath it. Topics for discussion Reducing cycle time- where to cut time and where not to Furnace fouling – temperature control and fire box flame patterns Soft coke vs heater fouling trade… The growth in domestic crude production, specifically tight oils, resulted in new challenges for refiners. Elevated levels of contaminant iron in crude are becoming the norm. Downstream, iron poisoning in… In our first Breakout webinar, participants will discuss the effectiveness of their site’s feedback loop, share successes and pitfalls, and learn from the experiences of their international operations colleagues. Sponsor: Many North American refineries have started increasing severity on gasoline posttreaters to make Tier 3 ultra-low sulfur gasoline. Our 3-year program of pilot plant and commercial field tests has shown that, when posttreater severity is increased, octane destruction will increase by much more than has been expected by the industry. Sponsor: The production of foam above the level of the coke bed during and after coke drum filling is just part of the process and is inevitable (generally). There are various scenarios where more or less foam can be expected. As part of this webinar, we will explore how foam can be reduced or managed with antifoam chemicals and through process awareness. Operator Training Simulators (OTS) have long been utilized to improve the skills of an operational workforce, thereby increasing plant performance… Sponsored Content Presented by CORYS Corrosion under insulation (CUI) is one of the best known and researched corrosion mechanisms in process industries. CUI is not often discussed in the context of the delayed coker specifically or especially around the drum structure equipment itself. Sponsor: In the beginning, the preferred valve of choice for delayed cokers was the lift plug valve. For many of you who still work on older units, you know this because all your valves are still this type. Sponsors: The heater charge pump is arguably the most critical pump in the entire delayed coker. It can also be the most challenging to keep properly ready in standby mode so it is hot and ready when called into action and QUICKLY. For many years, the only indication for the coke drum level was the Neutron-Backscatter (NBS) type. Then in the 90’s, continuous level gamma source instruments were developed. Their rollout has been gradual for the existing installed capacity and they are the standard on new grassroots units. Sponsors: Our goal is to keep the coke in the coke drum, right? We are not always completely successful in this mission but one way to keep the drum vapor line clean is to minimize carryover from the drum and quench the vapors “enough” to prevent coke deposition on the ID of the pipe. Traveling the coking world, we have literally talked to 1000s of operators and opinions vary about the ‘best’ way to switch the drum and steam strip. In this installment of eREFCOMM, we are going to investigate the variety of techniques in place and discuss the pros and cons of various methods. Thank you to everyone who attended and contributed to the discussion with questions, poll feedback and comments. It was a truly interactive experience. We can only get better from here….. Here are some recaps and critical insights shared during the event. With eREFCOMM, our goal is to recreate that community feeling of a live RefComm® event but in an online setting. Just like in the live RefComm events, the breakout sessions are ethereal and you have to be there to benefit from the information.DCU Process Breakout
DCU Process Breakout
Rethinking FCC Actuation and Controls
DCU Process Breakout
FCC Slurry Oil Filtration: Royal Dahlman has the filtration technology for the Oil Refiner and Trader to comply with the new IMO 2020 Marine Residual Fuels.
ROSE – Cost-effective and versatile solutions to improve refinery economics
FCCU Main Blower and Wet Gas Compressor UCP testing using Dynamic Modeling
Benefits and Challenges of Filter Cleaning in rFCCU and FCCU Processing Applications
Catalyst handling solutions for extreme temperatures in FCCU
DCU Process Breakout
Measures and Procedures to prevent Quality related issues during DCU plant commissioning and startup
Put Us In Coach – We Have the Experience to Increase B/CD by 10%
Solving Operational Readiness with Digital Tools for the Field Operator
Better DCU Performance through Smarter Insulation Design
SDA Technology 101
Anti-coking Solution for DCU Fired Heater Tubes
Silver Bullet: Reducing Torque in Dynamic Equipment
DCU Operations Breakout – Farmer Fixes
eREFCOMM – DCU Process Breakout – The Operator’s Guide to Successful Troubleshooting
Combating the Negative Effects of Iron in the FCCU at Philadelphia Energy Solutions
Proactive Maintenance/Design Practices for Coker Valves
Solvent Deasphalting: Why is there so much buzz?
How Effective are Operator Rounds at Your Site?
Octane destruction in FCC gasoline posttreaters
Managing Coke Drum Foam with Chemicals
Leveraging the Cloud for Refinery Operator Training
Should You Worry about CUI on the Coke Drum Structure?
Back to the Future: Lift Plug Valves Making a Come Back
Making sure your spare heater charge pump is ready for action
Coke Drum Level after the Demise of Neutron Backscatter (aka K-ray)
How Much Should You Quench Coke Drum Vapors?
Coke Drum Stripping Steam: A goldilocks approach
Understanding Coker Heater COT and TMT Measurement to Improve Your Unit Production