Facilitator: Michael Lemeshev, MOGAS Subject Matter Expert
Overview

FCC units process heavy gas oil or vacuum gas oil (HVGO) and convert them into much more valuable gasoline. Pressures are moderate, not exceeding 30-40 psig. Temperatures are very high, and in certain parts of the process can approach 1450 deg F. The “magic” of the FCCU is mostly contained with the catalyst that is utilized. This catalyst is highly engineered to produce specific output from the unit. Over time, this catalyst can degrade and must be replaced. Unit run times vary, but on average, FCC units have major turnarounds every 4-6 years. The catalyst must therefore be replaced with the unit in full operating mode.
An average sized FCC unit may process 60-80 KBPD. Units in this size range typically circulate 70 tons of catalyst. On average, 1-5 tons of catalyst may need to be replaced or restocked daily. Replacement is directly related to catalyst degradation, and restocking is related to the loses that occur due to normal FCC unit operations, like loses via the Fractionator bottoms slurry system if via the Regenerator flue gas system. Replacement occurs via catalyst addition and withdrawal systems. As the catalyst degrades it actually becomes more erosive. This is because the highly engineered particles, as they break up, now have extremely sharp edges. And, with the flow rates, in some parts of the unit, approach supersonic speeds, these degraded catalyst particles can wreak havoc on metallic components. That is why large sections of the unit are refractory lined. Not only does this refractory provide thermal protection, but it also provides erosion protection.
One place that the refractory lining does not extend into is the Catalyst withdrawal system. This system does continuous on-line catalyst removal from the hottest part of the process, the Regenerator, which operated at approximately 1450° deg F. Valves are utilized here, some for control service, others in pure isolation service. Different process licensors have different configurations, and methodologies, but all must remove some portion of used catalyst on a regular basis. MOGAS has provided our patented C-Series isolation ball valve in this exact service for many decades. MOGAS even overs a Performance Guarantee for these valves, a truly unequaled level of operational reliability. MOGAS utilizes specialty materials and coatings to give these valves, unprotected by refractory, long-lasting trouble-free service. Actuation is also part of the package, and MOGAS provides this as well, all specialty engineered and built to customer specifications.
MOGAS is the Dominant Severe Service Technology company, with isolation and control valve solutions and engineering services for applications such as delayed coking and catalytic cracking.
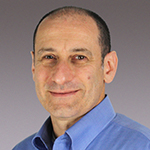
Refining and Petrochemicals, Michael Lemeshev has been in the refining and petrochemical industries for over 25 years and with MOGAS since 2014. While his industry experience includes product and project engineering and the design of flow control and isolation systems, he is most active in technical training and project execution by partnering with end users / refiners, licensors and engineering companies to bring total solutions.
A graduate from Texas A&M University with a BS in mechanical engineering, Michael has been a contributing subject matter expert for industry publications.