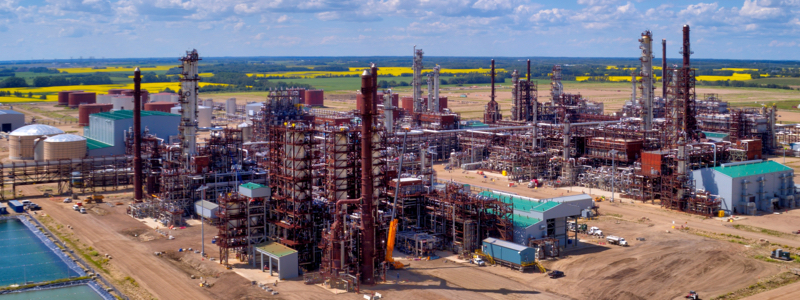
Resid HydroCracking is quickly emerging as today’s hot refining technology to increase bottom of the barrel conversion. Although this process has been around for 50 years, it only recently gained popularity because of its ability to process heavier and diverse feedstocks and reduce sulfur content. The Sturgeon Refinery shown in the cover image above commissioned their RHC in December 2018. There are 25 active sites according to this infographic by MOGAS.
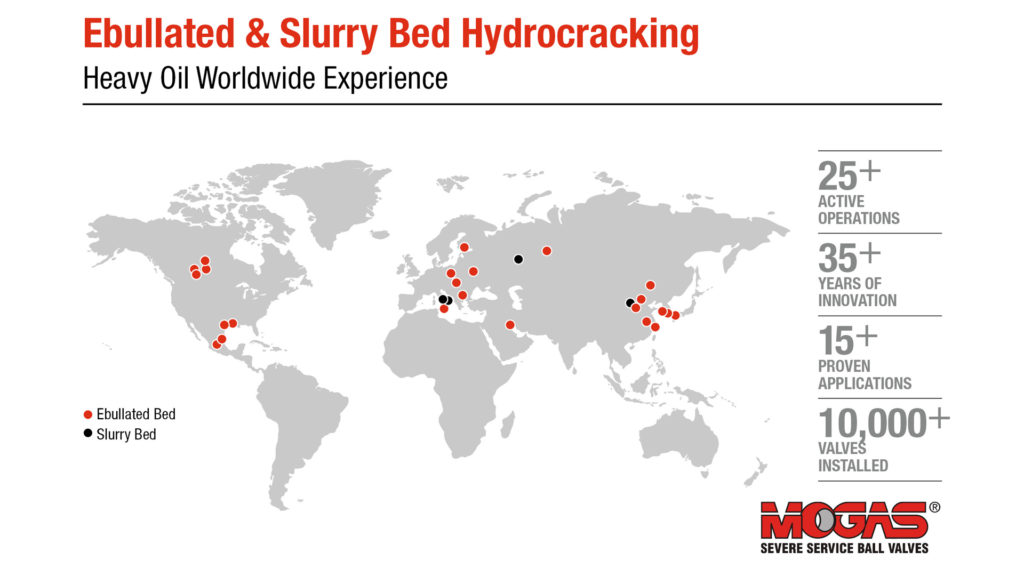
As a result of Residue Hydrocracking’s growing importance, Refining Community now offers the first worldwide conference and user’s group for any licensee to address this process.
For people wanting to learn more about the RHC, you participate in a ‘boots on the ground’ approach to operations, engineering, maintenance, inspection, and design. You’ll openly discuss issues and solutions that are common across the various licensors and unit configurations.
For example, high-temperature fouling of heat exchangers and let-down valves are common across all types of RHC units. The best practices to predict, prevent, and maintain this equipment from fouling falls under the safety banner, because the less often we must interact with the equipment, the fewer opportunities for risk to personnel are expected. You’ll hear lots of other examples during the RefComm® Galveston Conference and Exhibition.
Whether you use Axens H-Oil, Chevron Lummus, ENI EST, Hebei Xinqiyuan Shanghai New-Unity, Shell HYCON, KBR VEBA or UOP Uniflex™MC™, or a custom process, we’ll seek common ground, where possible, so that solutions developed after more than 20 years of operating in an ebullated bed unit can be applied to a slurry-phase or fixed bed unit.
Leave a Reply