—By Dan Gillis, Director, Technology, Chevron Lummus Global
This article was adapted from Dan Gillis’ presentation at RefComm® Galveston 2019.
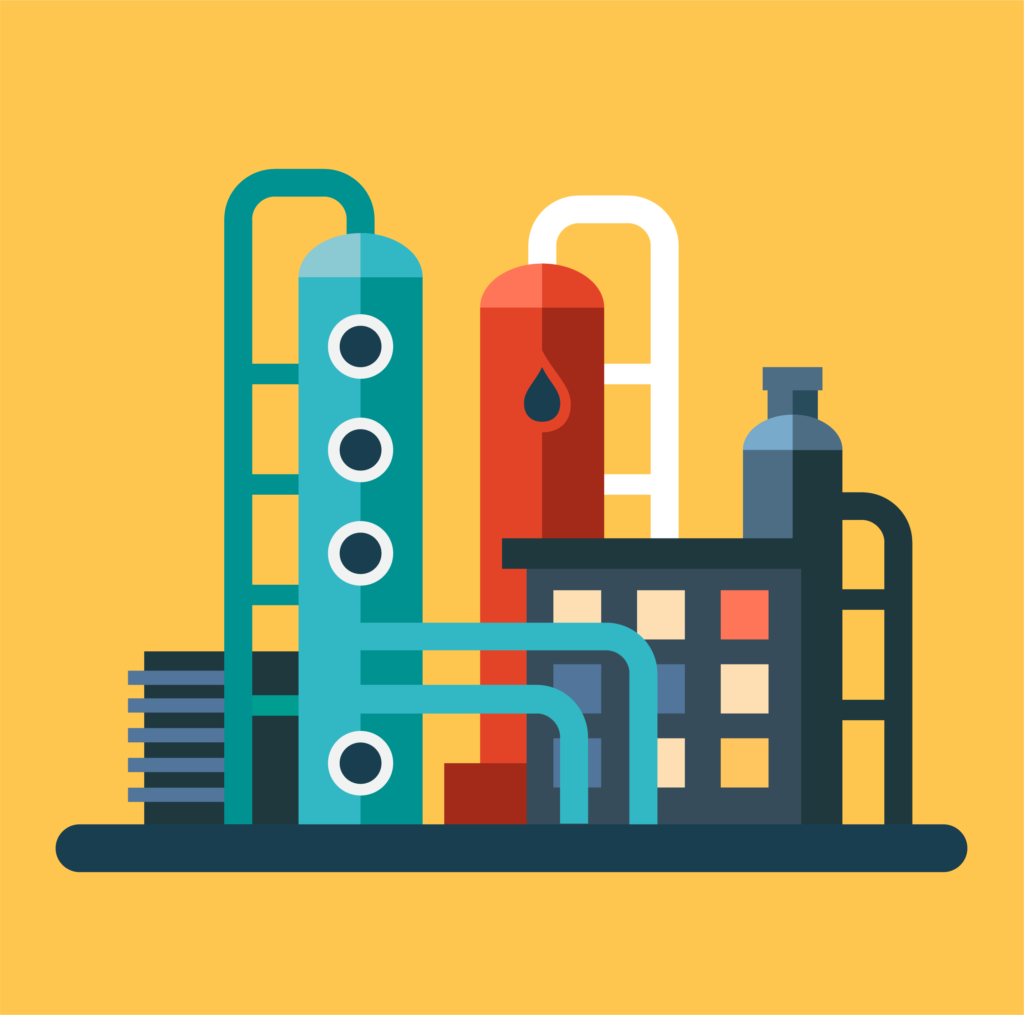
Residue Hydrocracking (RHC) has gained traction as the desired residue conversion process in recent years. Several new world-scale projects are being based on RHC, not only for residue upgrading and production of transportation fuels, but also for crude to chemicals projects, and even in the production of Low Sulfur Fuel Oil (LSFO).
One of the world’s leading technology partnerships, Chevron Lummus Global (CLG), a joint venture between Chevron and McDermott, is in a unique position to discuss the merits of RHC as it actively supplies all forms of residue conversion technologies. Over the years Chevron has demonstrated a high level of hydroprocessing in its refineries. It operates more than 100 high-pressure hydroprocessing reactors and in the U.S., Chevron operates six ISOCRACKING units and four delayed coking units. CLG’s RHC technology, LC-FININGTM (Lummus Cities reFining) was developed by Lummus Crest and Cities Service Research and Development Company in the 1960’s, initially for upgrading bitumen from tar sands.
CLG has expanded LC-FININGTM’s applications by combining it with other technologies such as coking and solvent deasphalting (SDA) and with the use of dispersed catalysts to provide cost-effective high conversion solutions. Key to the application of RHC is the assurance that this process is reliable, which has been confirmed through continual feedback from the commercial units and advances in equipment and designs.
This article provides not just an overview of RHC and its merits for maximizing a refinery’s profitability, but also its impact on a refinery’s capability to produce various products and flexibility for future needs. A comparison of flow schemes is also provided to show how RHC can be integrated into a refinery to maximize production of gasoline, propylene, as well as petrochemical feedstocks.
Future Market Requirements
Market pressures are driving residue upgrading solutions to high conversion. The demand is higher for PetChem than for transportation fuels. But transportation fuels and LSFO still enjoy a relatively strong demand, whereas the demand for HSFO and coke are weak. All of this points to residue hydrocracking as the best fit to meet all the requirements.
LC-FININGTM
The LC-FININGTM Residue Hydrocracking process meets future product demands due to its high conversion capabilities and ability to process a wide range of residues. Stand alone LC-FININGTM units commercially now achieve conversion levels upwards of 85% with associated contaminant removal and product quality upgrading.
The ebullated bed residue hydrocracking technology platform has several reactor features which set it apart. It contains an upflow reactor and a low pressure drop. A recycle pump backmixes and expands the single catalyst bed. It is nearly isothermal and the catalyst can be added and withdrawn online.
The LC-FININGTM Reactor Platform
Downstream of the reaction system is an energy-efficient multiple step separation and fractionation section required due to the challenges associated with a high conversion residue hydrocracking process.
The LC-FININGTM Product Separation and Fractionation System
Why is Conversion Limited in Residue Hydrocracking?
Part of the reason for conversion being limited in RHC is due to the asphaltenes and CCR in the vacuum residue. As we push conversion, we have to convert more and more difficult types of asphaltenes. There is also the challenge of managing sediment formation, which increases at higher conversions. Feed properties have great impact on conversion.
Managing Sediment is the Key to High Conversion
Some sediment reduction options include:
- aromatic diluents
- additives/co-catalysts
- catalyst advances,
- and flow scheme solutions.
Aromatic Diluents have proven to improve solvency and reduce sediment. Key to their use is the type used, operating conditions of the reactors, and injection locations. Some units have seen 2-3% conversion increase with them.
The results are mixed when it comes to co-catalyst benefits. Several units have witnessed severe fouling under reactor distribution grid when using a co-catalyst. And with soluble molybdenum co-catalysts, the type of pilot plant is important in determining the benefits as expected performance improvements can be misleading with typical small back mixed pilot plants.
CLG has worked closely with two of the company’s licensees who had chosen to inject organo-moly into their feed. Unfortunately both of these units experienced severe under grid fouling in the first LC-FININGTM reactor. Extensive analysis of the under grid fouling deposits shows them to contain a high percentage of moly, but little to no alumina. A third LC-FININGTM unit which has processed feed containing naturally occurring organic moly has also experienced sever under grid fouling in the first LC-FININGTM reactor.
Higher Conversion is enabled with the appropriate catalysts and operating conditions
There is a conversion-sediment tradeoff pattern and higher conversions can be obtained with advanced catalyst formulations, dual catalyst systems, and optimized operating conditions. This has been demonstrated not only in pilot plants but also in commercial units.
Catalyst Advances Allow High Conversion
LC-FININGTM Flow Scheme Solutions increase Residue Hydrocracking Performances. This is being applied commercially in several ways resulting in significant conversion increases compared to standalone LC-FININGTM operations.
Options | Solution Examples |
Processing LC-FININGTM UCO in a delayed coker | Unit C LC-FININGTM UCO is processed in a coking unit with overall conversion >88% |
Modifying feedstock such as with an upfront SDA | Unit D SDA unit on part of LC-FININGTM feed boosts conversion boosting conversion by 10% |
Selective conversion of feedstock components | LC-MAX flow scheme to obtain >93% conversion – selected for several new units |
Converting low value UCO into high value LSFO or FCC feed | Integration of CLG LC-FININGTM + RDS technologies has been designed already for one European client |
Utilizing advanced micron sized catalysts | LC-SLURRY advanced slurry hydrocracking to maximize high value products results in over 95% conversion and no production of low value residues. First license is in engineering phase and will have a LSFO byproduct |
Residue Conversion Addition Impact on Refinery Yields
CLG has studied extensively the application of this powerful technology in both refinery and crude to chemicals settings. Depending on the application and project objectives a significant increase in a plant’s high-value product yields can occur. For a recent client study CLG undertook it was validated that the high-value product yields could increase from 16 to over 21 % of crude oil feed stock.
SUMMARY
The benefits of residue hydrocracking are many as evident with industry now selecting this technology at similar levels to thermal conversion technologies. This is due to the technology evolvement into a refinery leading reliable process that obtains the highest conversion and liquid yield levels. Additionally, its flexibility and ability to incorporate integrated hydroprocessing within the unit has resulted in it is now the preferred choice of refiners to meet future product requirements.
You can download Dan Gillis’ full presentation here. Click here for more information on RHC. We will be offering a Resid Hydrocracking track at RefComm® Gdansk 2020. For more information, visit https://refiningcommunity.com/refcomm-gdansk-2020/
___________
About the author
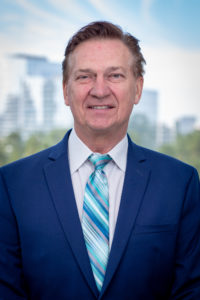
Dan Gillis is the Director of Technology for CLG. In this role he provides technology business development and new technology commercialization for CLG’s residue conversion technologies with a focus on high conversion residue upgrading applications, including coking, LC-FININGTM, LC-MAX® and LC-SLURRY. Dan also provides consulting to CLG’s customers on their residue upgrading technology selection and project configuration studies.
Prior to joining CLG, Dan held business management, technology sales management, and engineering management roles for Foster Wheeler and UOP LLC, primarily with their heavy oil processes. Previous to UOP he held various business development, technology development, operations and process engineering roles in refining and heavy oil upgrading organizations. Dan is a 1977 engineering graduate of the University of Saskatchewan, Canada.