By: Alex Mathew, Assistant Manager (Maintenance – Rotary)
Bharat Petroleum Corporation Ltd. – Kochi Refinery
This article is applicable for pumps in the DCU, as well as any other units LPG/Propylene is handled.
Introduction
From the history of some LPG/Propylene pumps in CDU and FCC units, it has been noted that some of the seals are not providing the desired life of 3-4 years. Detailed investigation and efforts were put into conducting the RCA and finding the solution.
This can be generalized for pumps handling highly volatile and inflammable fluids like propylene, LPG, etc. barrier fluid is provided in the secondary seal. In mechanical seals handling these fluids, the seal configuration will be as per API 682 Arrangement 3 (3CW configuration) with only secondary seal plan irrespective whether seal face arrangement is Face-to-Back, Face-to-Face or Back-to-Back). For process applications handling critical fluids, an externally supplied fluid at a pressure above the pump seal chamber pressure, introduced into an Arrangement 3 seal to completely isolate the process liquid from the environment.
What happens if heat generated is not removed?
The generated heat from the seal faces is removed by the barrier fluid that circulates through the seal flushing chamber and is rejected at the heat exchanger. If the heat rejection is not proper, it can cause temperature rise of the fluid and will result in coking of the oil at seal face and increases the wear of the seal faces.
Also, for the primary seal, if the stuffing box pressure and the vapor pressure of the fluid are very close as it tends to cause a dry run at the seal faces due to vapor formation if heat rejection is not proper.
The seal faces that are removed while overhauling are shown in the below picture.
Below picture shows the black particles formed due to wear as well as coking of oil.
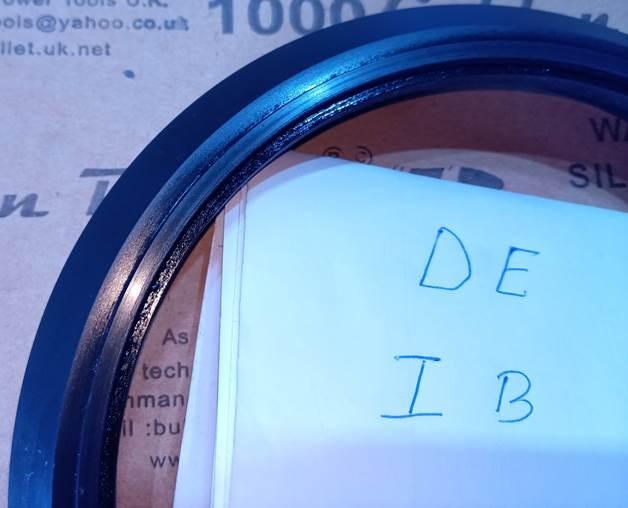
Below picture shows a wear pattern due to excessive wear.
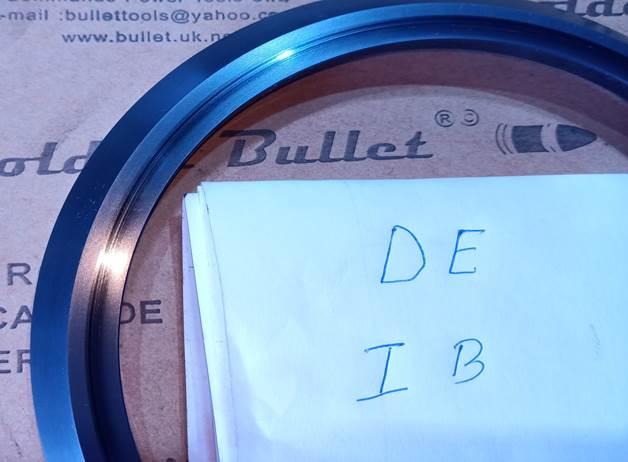
Limitations that can cause failures
In general, 3CW configuration is provided with no primary flushing plan as heat generation is relatively low compared to 2CW configurations.
However, the only way to remove the generated heat from seal faces is through the heat rejection at Plan 53B cooler. Thus, the adequacy of the cooler and its design is most important for reliability and enhanced life of the mechanical seal.
Following are some issues that can reduce performance of the Plan 53B seal cooler:
- Fouling
- Issues with cooling water header pressure
- Back pressure issues in cooling water return header
- Increase in cooling water supply temperature
Due to above stated reasons the cooler designs may not give desired performance.
The methods that can be adopted for maintaining the seal temperature are:
- Increasing heat duty of Plan 53B cooler.
- Providing cooling facility for stuffing box (if provision is available on the pump).
- Checking feasibility for providing a primary flushing plan (if 3CW-FB configuration).
Very useful article
Muhammed, thank you for your comment- we are glad you find it useful!
Great article and useful information
Very informative