Throughout its 40 years of operation, Blasch Precision Ceramics has engineered custom ceramics shapes to replace monolithic structures, such as brick-n-mortar, castable, plastic refractory or gunnite. The company was recently hired to replace a metallic part for a refinery client with a ceramic shape to address wear, corrosion or high temperature degradation. Blasch is no stranger to this task, having successfully completed similar projects for other refinery clients over the years.
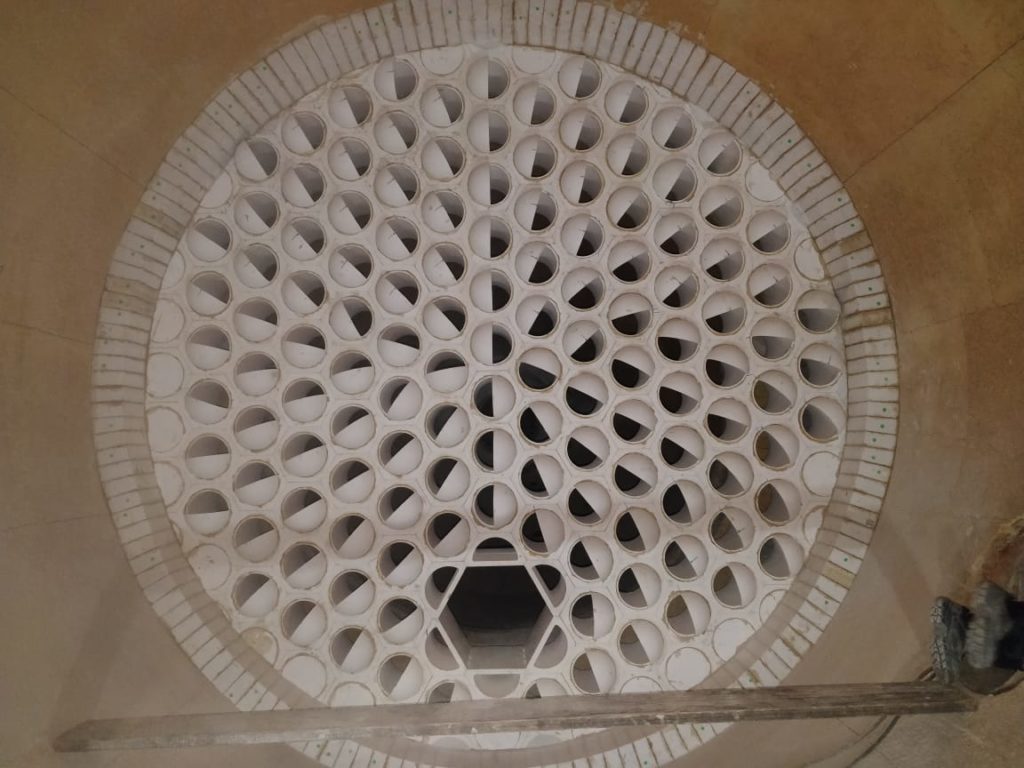
For hundreds of years monolithic refractories have been employed to provide insulation, corrosion and abrasion protection. Over time through thermal cycling these monolithic assemblies tend to crack, spall and crumble apart. Large chunks of refractory will eventually crack– it’s inevitable. For the same reason you put an expansion joint in a concrete patio or a roadway, you must provide areas where ceramics can relieve the stresses that are built up. Blasch engineered those “cracks” for its client ahead of time, creating tortuous paths and engineered joints, and thereby eliminating the stresses that would eventually turn into failures.
By producing these parts in a controlled and repeatable process along with computer-controlled firing cycles, Blasch achieved advertised material traits and eliminated the unknown. Knowing how long something will last provided the client with a predictable turnaround schedule, which in turn helped to increase refinery production.
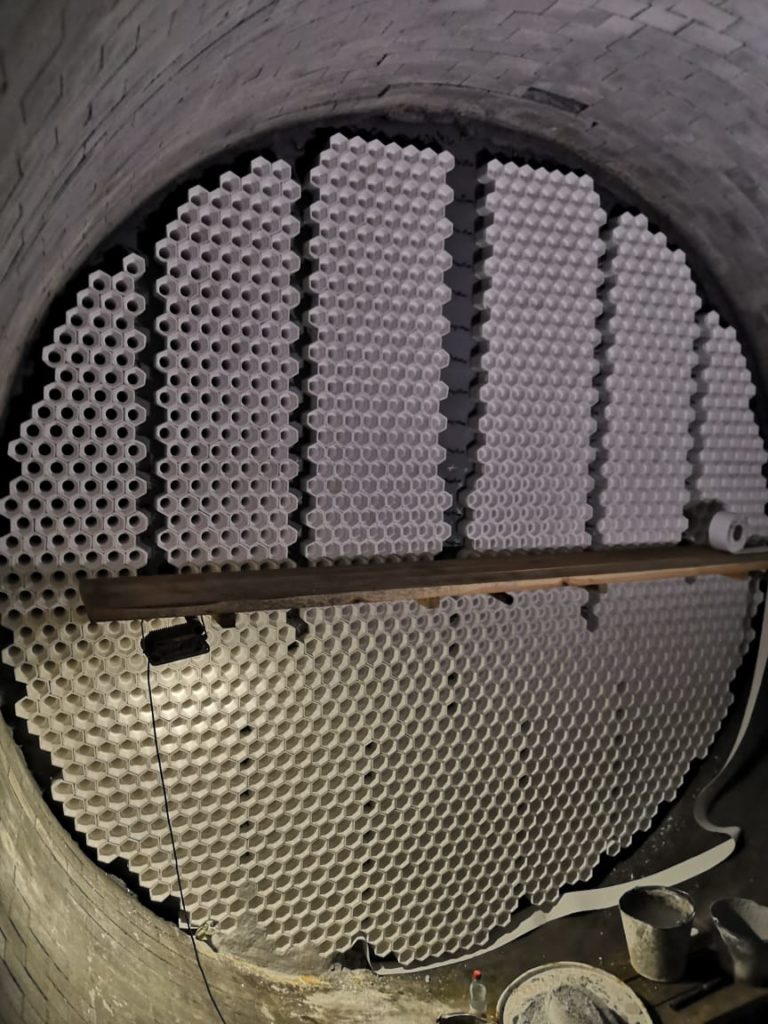
Oftentimes, when an installer or user purchases someone else’s bag of material and does not mix it properly or add the right amount of moisture/binder, the results can be sporadic. Blasch’s net shape casting process removes these doubts and inconsistent nature of refractories and ceramics.
For the last 25 years Blasch has addressed problems with monolithic refractories and brick constructions in refineries. The company replaced round boiler tube ferrules and castable with its HexProTM Ferrules, brick-n-mortar checkerwalls with its HexWallTM Checkerwall assemblies, and brick-n-mortar reformer tunnels with its StaBloxTM Tunnel Assemblies. In all of these instances, what started out as a simple means to address maintenance and reliability, turned into so much more. The company learned that a simple static chunk of refractory can actually improve the process and provide more yield and throughput for the refinery if subtle design tweaks were implemented.
A lot of companies get so accustomed to replacing and repairing something repeatedly, that they never sit down and ask themselves if there is a better product or design out there. That is where Blasch’s engineers come in, and they evolved Blasch’s line of products, which led to the development of ProLokTM Ferrules, VectorwallTM Assemblies and StaBloxTM with TOPTM.
In the fluid catalytic cracking units (FCCU’s), Blasch employed that same approach. Having developed AltronTM – an alumina bonded silicon carbide that has ASTM C-704 abrasion resistance in the 1.5cc range, the company can address areas of the catcracker that are seeing excessive wear. It’s well known that the go-to material in the catcracker is a hexmesh castable. Welded steel anchors in the form of a hex shape are welded into place. Then a castable/monolithic material is mixed and cast within the metal openings. It is then cured by applying heat. Although the posted wear numbers are in the 2-4 cc loss range, quite often all it takes is a few percentages off in moisture, improper mixing, humidity, time and temperature to cure, to affect these values.
Blasch has provided the industry with shapes such as Grid Nozzles that have successfully replaced high alloy metallic nozzles, often extending the life two-fold. Recently the company was approached by two separate refineries to address an abrasion problem in their scrubbers. Although the client could have easily recommended and installed a hexmesh castable, they wanted something better. Blasch sat down with the refinery and the engineering firm to come up with a stud welded pre-cast AltronTM Silicon Carbide Tile. The tile had interlocking joints that, when assembled, provided a smooth wear surface and prevented material, such as coke and catalyst fines to work their ways through the joints. By providing the customer with a pre-cast, controlled product that has engineered joints to allow for thermal growth and contraction, it provided the best of both worlds. As well, if the client ever needs to replace a component or do any repairs or inspections, they can easily remove and replace a tile without disturbing the surrounding components. The refinery can often do this on their own without hiring a separate refractory contractor. Blasch was able to eliminate the need for a skilled laborer or bricklayer.
Blasch will be exhibiting at RefComm® Galveston 2020, with a focus on their engineered shapes to address a problem with high temperature, corrosion or abrasion in the fluid catalytic cracking and sulfur recovery units. You can visit them at Booth 10 and in the meantime, you can learn more about them on their website: https://www.blaschceramics.com/
Leave a Reply