For decades, plumbers have thawed frozen water pipes by connecting portable welder electrodes to both ends of the frozen section and running a low-voltage current through the pipe. Effectively, the pipe becomes a heating element, melting the ice inside. That, in its simplest form, is impedance heating.
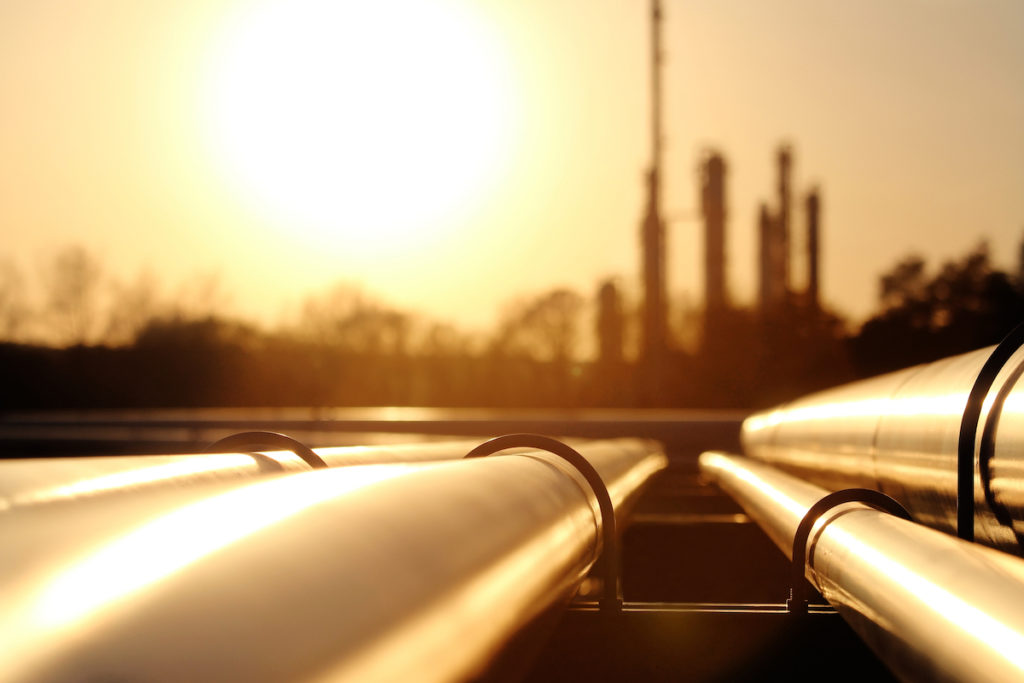
How Impedance Heating Works
In industrial applications, a multi tap a.c. transformer supplies low-voltage current to a pipe transporting a gas or liquid. Cables and a control panel are connected and the heated pipe is electrically isolated. Terminals are attached to each end of the pipe, and a low voltage current is passed through it, allowing the pipe to act as its own heating element.
When to Use Impedance Heating
Impedance systems heat a wide variety of gases, liquids and viscous materials which are stored, pumped and processed in many different industries and applications. Impedance heating can be used in three basic ways:
- Cold Start: Heat is applied to increase fluidity of static, viscous materials so they can be pumped. Typical materials include asphalt, molasses and heavy fuel oils.
- Maintain Temperature or Pipe Tracing: Heat is applied to a liquid or gas flowing through a pipe to offset heat losses. Typical applications include freeze protection or maintaining the fluidity of viscous materials.
- Temperature Rise: Heat is applied to a liquid or gas flowing through a pipe in order to raise its temperature between the inlet and outlet of the heated pipe. Typical applications include heating corrosive liquids or high temperature process air.
Benefits of Impedance Heating
- Low Voltage Operation: All systems operate at less than 30 Volts, many at 10 Volts or below.
- Uniform Heating: Because the entire pipe effectively acts as the heating element, heat is generated uniformly throughout its entire length and circumference without hot spots.
- Simplicity: The impedance method takes the complexity out of pipeline heating. A few basic components comprise the entire heating system. Installation is simple; it can be installed without disturbing most of the existing thermal insulation.
- Close Control: Thermocouple sensors placed along the pipeline provide precise, uniform temperature control. Optional SCR controls give the ability to achieve control within ± 1o F.
- Low Cost: Installation costs are kept to a minimum by the inherent simplicity of the system. Likewise, maintenance is virtually eliminated; many systems operate unattended. Energy costs are low because the required energy is concentrated in the pipe and efficiently heats the fluid or gas traveling through it.
- No Burnouts: When the pipe becomes the heating element, burnouts and failures associated with electrical resistance tapes and cables are eliminated.
Advantages of Impedance Heating Over Conventional Methods
- No External Fluids: Pipeline heating with steam or high temperature fluids introduces a high degree of complexity and a potential hazard. Impedance heating accomplishes the same result in a simple, straightforward manner.
- No Leaky Jackets: With impedance heating, there are no leaky steam lines, cracked steam traps, pump failures or frozen return pipes.
- No Hot Spots: Impedance heating eliminates the danger of overheating temperature-sensitive materials because hot spots associated with conventional pipe tracing are eliminated.
- No Routine Maintenance: Routine maintenance is eliminated, along with the replacement parts and production shutdowns associated with such maintenance.
Indeeco specializes in impedance heating solutions across a broad range of industries, including the oil and gas sector. A few years ago, a refinery client tasked Indeeco with replacing two lines of existing impedance heated piping. The existing system transferred crude tar and other products. This system had been in place for 30 years and the client had been meaning to update it for some time but kept putting it off. Needless to say, the project Indeeco was tasked with had a certain sense of urgency to it.
Indeeco deigned an impedance system for the client’s new pipe lengths, which had been shortened by 30% from its original system. Each line consists of two center tap impedance systems using 500 MCM cables evenly divided. Each of the four heating systems used 25 KVA transformers, 480V primary with six tap secondary 22 to 32 V.
Indeeco was able to meet the time constraint, supplying the equipment in record time and installing the new parts while maintaining the exact same temperatures for the system. This allowed the client to maintain production and saved them thousand of dollars they would have lost in down time.
Indeeco will be exhibiting at RefComm® Galveston, so be sure to stop by Booth 64 to learn more about the benefits of impedance heating. To register for RefComm Galveston, visit: http://www.cvent.com/events/refcomm-galveston-2019/event-summary-bb85ca75834f4dcda66da9ae14b402a0.aspx. Early bird pricing ends March 18!
Leave a Reply